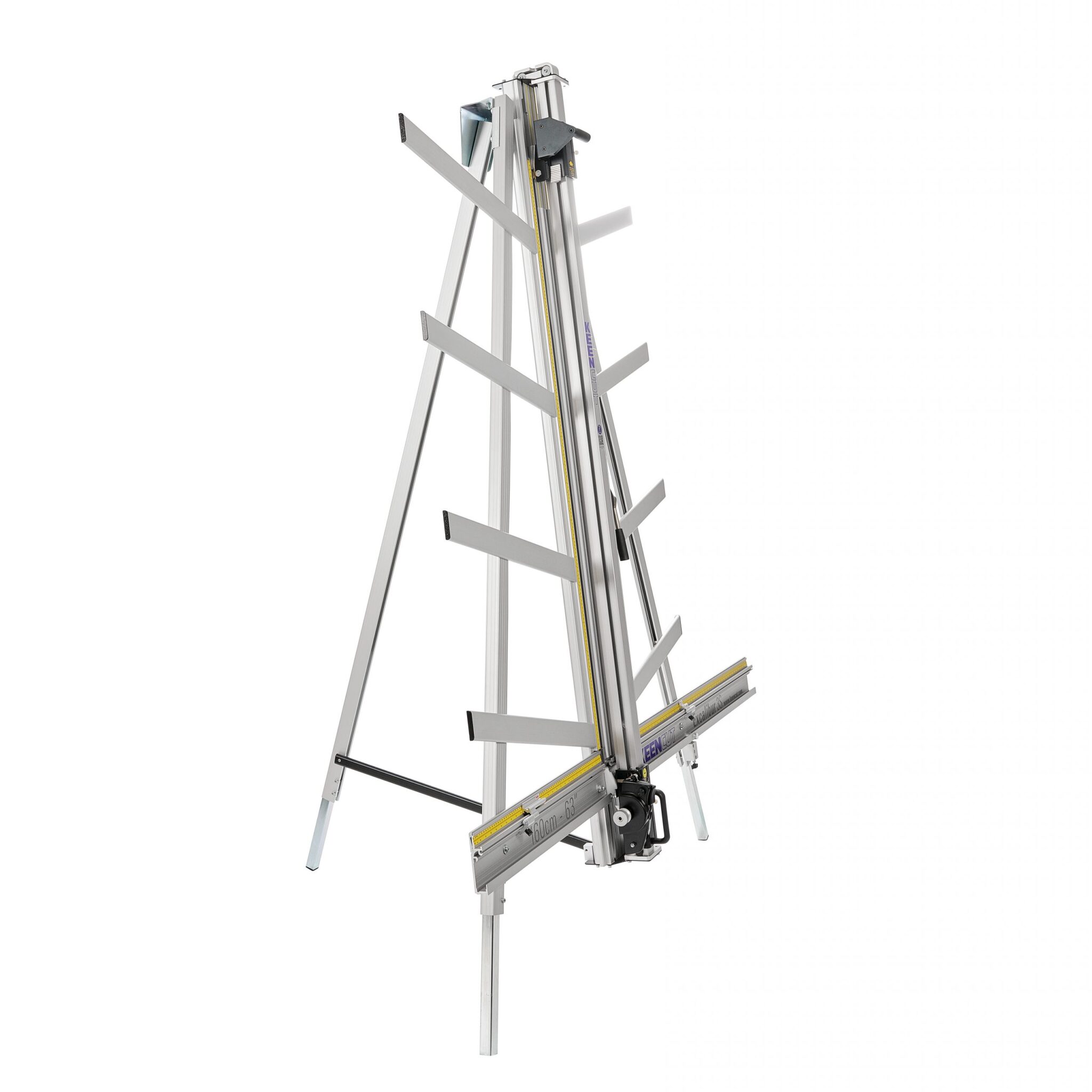
Scroll down to view the guide.
You can expand and collapse sections using the + and – icons.
View PDF version >
Register your cutter to activate your guarantee >
Visit Keencut support centre >
Visit user forum >
Installation video >
Contact Keencut >
This User Guide for the Excalibur 3S gives advice on cutting techniques, care and maintenance of your machine.
Before using your machine make sure that you have installed and calibrated it correctly. Full details are in the Installation Manual.
The clamping system enables the operator to control the grip pressure by means of an integral friction brake, that maintains the clamping force at the pressure applied by the operating lever. Soft materials can be held firmly without sustaining damage and solid materials are held rigidly without movement. By following the guidelines below it will help you to get the most from the machine.
Soft materials such as Foamcore boards, lightweight card, etc. Use light to medium pressure. The underside of the clamp grips an area nearly 4cm (11/2”) wide with a non-marking sponge rubber
and reasonable force can be applied. If in doubt clamp a sample first with the good surface facing outwards.
![]() |
Do this gently |
For harder materials such as PVC foam board, MDF or composite boards such as Diabond, use medium to heavy pressure.
![]() |
Do this firmly |
When cropping to trim lines, pencil marks, etc. (see drawing), place material in approximate position under clamp, apply light clamp pressure to allow the material to be repositioned. Align the trim marks with the edge of the sightline strip and clamp.
The Excalibur 3S is fitted with two sliding carriages running on a vertical slideway and each carriage is fitted with a cutting head. The top carriage is fitted with a twin wheel cutter for use with rigid boards such as aluminium composite panels, MDF, hardboards. Refer to Changing the twin wheel cutter > or Using the twin wheel cutter > for more details. The lower or multi-tool cutter head has a rotating turret arrangement where either of the two cutting tools can be selected (the cutting blade or the scoring blade).
To select a different cutter pull the turret handle out to the left about 6mm (1/4”) and rotate in either direction, the turret will click into the correct position for the cutter indicated. Please note that there are three positions on the turret but only two positions are used on this version of the Excalibur.
The indicator label seen in the cutter guard window shows which cutter is active.
The counterbalance can be attached to either cutting head for easy, fatigue free working. it is normally attached to the twin wheel cutter but to attach it to the multi-cutter head, lock the twin wheel carriage in place using the white plastic thumb screw. Raise the multi-cutter to engage the counterbalance rocker, press the lower head of the rocker to connect it to the carriage.
Select the cutting blade position on the turret and clamp the material in the machine. Move the cutting head beyond the top of the material to be cut.
Press to engage the cutter. Draw the cutter down to the bottom of the machine where it will disengage automatically.
Should you engage the cutter by mistake or for any reason want to disengage the cutter without moving it to the bottom of the machine pull down the cutter and release lever.
The two support plates either side of the blade are designed to give maximum rigidity of the blade when cutting hard or dense materials. To adjust the support plates swing down the cutter guard by undoing the guard locking knob. Turn the turret ½ turn until blade is pointing towards you.
Unlock the blade clamping screw.
The support plates can be adjusted by sliding the black pin in the slot. Move the plates to suit the material and tighten the clamping screw once the support plates are in position.
To change the cutting blade, undo the blade clamping screw a number of turns to release the blade.
Change or turn over the blade, insert it back into the turret as far as it will go. Tighten the blade clamping screw, the safety pin will engage to hold the blade in position. At this point the position of the blade support plates can be adjusted to suit the thickness of material being cut, further tightening of the screw will clamp the blade in position.
Rotate the turret back to the cutting position. Replace the guard ensuring it is locked closed.
Unlock and swing down the cutter guard, rotate the turret so the scoring blade is facing outwards.
Release the blade clamping screw
Eject the medium duty utility blade using the black ejector pin, replace the blade to the right of the clamping plate, push the blade in as far as it will go and tighten the blade clamping screw. Rotate the turret back to the cutting position. Replace the guard ensuring it is locked closed.
Lock the cutting head at a convenient height using the white nylon locking screw.
Hold the twin wheel cutter and its guard to prevent them from falling and remove the screw with a 6mm Allen (hex) key. Slide the cutter towards the top of the main body and lift out.
A unique feature of the Excalibur is the ‘ratchet latch’, this enables thick dense materials such as PVC foam board to be cut easily in stages. Count the number of ‘clicks’ to position the blade just below the surface of the material to make your first cut then add an extra ‘click’ for the second and subsequent cuts.
As a rough guide when cutting PVC foam board:
3MM (1/8”) Initial surface cut + 1 additional cut
5MM (1/4”) Initial surface cut + 1 or 2 additional cuts
10MM (3/8”) Initial surface cut + 3 or 4 additional cuts
Should you engage the cutter by mistake or for any reason want to disengage the cutter without moving it to the bottom of the machine pull down the cutter release lever.
For some operations (such as scoring acrylic) the ratchet latch needs to be disengaged, so that finger pressure is used to make the score/cut. This is done by pulling the black knob on the edge of the spring spool down to face towards the user. To re-engage the ratchet latch push the small black knob away so it points upwards.
NOTE : The scoring blade is designed to score acrylics, Plexiglas and other similar rigid plastics. Trials should be carried out on scrap materials first to ensure you obtain the required standard of cut.
Select the scoring blade position on the turret and clamp the material in the machine.
Turn the ratchet hold-off knob to disengage the ratchet.
Clamp the plastic to be scored in the machine, position and depress the cutting head so the blade touches the plastic at the top. Apply thumb pressure to the cutter and draw the blade down the material in one continuous motion
Remove the plastic from the machine and snap it by hand.
The twin wheel cutter is mounted on the upper cutting head and is used for cutting rigid materials such as aluminium composite panel and MDF up to 3mm (1/8”). Many other softer boards and card can also be cut, trials should be carried out to ensure the desired quality of cut is obtained.
Position the material in the machine and apply the clamp.
Bring the twin wheel cutter down until it makes contact with the sheet edge and stop. Take a firm grip and then push the cutter down through the material without stopping.
The cutting wheels generally last more than a year with average use but this is dependant upon daily use and the material being cut.
The signs the wheels are wearing out are:
1) A rough finish predominantly on the right hand side of the cut, with flaking on material such as MDF.
2) The bottom of the cut bursting out rather than being cut neatly.
3) The board trying to turn under the clamp when being cut (also check the clamp pressure).
Do not wipe the squaring arm channels or remove any debris with fingers, as it may contain sharp particles such as glass.
Use a vacuum cleaner if possible or if a soft brush is used, work slowly and do not allow particles to flick off the bristles.
The slideway can be cleaned and lubricated occasionally using a silicone lubricant. Removing any excess with a cloth.
The multi cutter assembly may require dusting out periodically do not lubricate or adjust without seeking further advice from your distributor or Keencut.
Attach the balance weight (see The multi-tool cutter and the counterbalance >) to the other cutting head, hold the cutter at waist height and place a 2mm hexagon wrench on the top adjustment screw.
Move the cutting head up and down and tighten the screw very gradually until the cutting head does not fall under its own weight.
Loosen the screw by the smallest amount you can until it does fall under its own weight. Repeat the process with the other three adjustment screws (A).
Move the head to a comfortable height.
Apply the balance weight to the lower head.
Tighten the white screw on the upper head.
Move the lower head away from the upper head.
Use a 6mm Allen (hex) key to remove the screw holding the twin wheel cutter in place. Slide it up to the top of the machine and remove.
Use a 2mm Allen (Hex) key to remove all 8 screws from the handle.
Hold onto the handle, remove the white screw, and move the head up and down carefully. The two bearing blocks should drop out.
Rotate the head until it comes loose from the machine.
Use a 2mm Allen (Hex) key to remove the screws holding the internal bearings in place.
Reverse these steps to re-install. Refer to Adjusting the sliding bearings> to adjust the sliding fit.
The pressure of the clamp is in relation to the amount of pressure applied to the operating handle. However in time the maximum clamping pressure can reduce due to wear on the friction black (hidden within the machine), compensation for this can be made by adjusting the two small grub screws in the operating handle housing as shown. Turning the screws clockwise will increase the maximum clamping pressure.
Turn both screws all the way in and then undo by a quarter of a turn, slight adjustment can be made to fine tune the pressure. Do not operate the clamp with the adjustment screws tight.
The sightline strip is fixed to the clamp and then trimmed using the cutting blade to give an accurate guide when cutting to trim lines, the edge of an image or pencil marks.
NOTE: Do not engage the twin wheel cutter until after reading its instructions for use in Using & changing the twin wheel cutter>. Engaging the twin wheel cutter interferes with the sightline strip and can cause damage to it. A gap is left in the sightline strip at a convenient height to enable the twin wheel cutter to be engaged.
Remove the worn sightline strip by peeling it off and clean any surplus adhesive with solvent cleaner on a cloth. Remove the backing paper and starting at the bottom press the strip firmly in the channel provided working upwards and cut off at a convenient height. Leave a gap of 18cm (7”) and then fit the remainder of the strip.
Place a piece of firm board up to 6mm (1/4”) thick on the machine to bridge the gap running down the back of the main body, this needs to be the full height of the clamp.
Place a piece of card or foam board 3-6mm (1/8”-1/4”) thick under the full length of the flexible part of the sightline strip, not under the aluminium clamp itself. Depress the clamp handle so that the sightline strip is pressed flat across the surface of the board.
Keep fingers clear and using a block or tool hold down the top left corner of the strip to start the cut. With the turret ratchet disengaged (see Using the scoring blade >) press the blade lightly on to the surface of the sightline strip and score along the full length. Repeat and trim the sightline strip in 2 or 3 cuts.