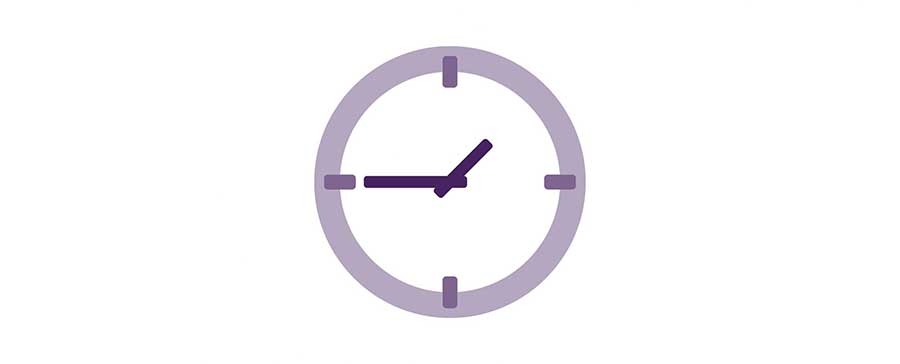
Scroll down to view the guide.
You can expand and collapse sections using the + and – icons.
The images in this manual are expandable. Click/tap on them to enlarge.
View PDF version >
Register your cutter to activate your guarantee >
Visit Keencut support centre >
Visit user forum >
Contact Keencut >
The Evolution3 SmartFold (part A) comes in 6 different sizes ranging from 1.1m (44″) to 3.6m (144″)(cutting length) in 0.5m (20″) increments. Each machine is fitted with a Double Graphik blade cutting head.
E3SF110: 3 x B 6 x C
E3SF160: 4 x B 8 x C
E3SF210: 5 x B 10 x C
E3SF260: 6 x B 12 x C
E3SF310: 7 x B 14 x C
E3SF360: 8 x B 16 x C
The three pieces of ACP (aluminium composite panel) or PVC foamboard should be approximately 150mm x 100mm (6″ x 4″) and 3mm (⅛″) thick.
In this section you will need base brackets (part B) and short socket head screws (part * – delivered with the SmartFold Bench).
Place the first base bracket (part B) 12cm (4 3⁄4″) from the edge of your SmartFold Bench. Use the 4mm Allen (hex) key to tighten screws (part *).
Place the following base brackets (part B) 43.5cm (17 ⅛”) from the edge of the previous base bracket. Use the 4mm Allen (hex) key to tighten screws (part *).
Continue placing the rest of the base brackets in this way.
Centralise and lower the cutter slowly onto the base brackets.
Ensure the holes on the arms of the cutter (highlighted in image) are aligned with the holes in the benches support plates.
Once the SmartFold is in place, use scissors to remove the film packaging.
The base brackets have 2 grub screws each located at the front and the back (see ‘ x’ and ‘ y’).
Use the long end of the 3mm Allen (hex) key rotate the grub screws in the front of the base brackets until you feel them come to a stop, do not tighten any further.
Do this gently |
Repeat the process on the grub screws at the back of the base brackets.
Do this gently |
Use the 3mm Allen (hex) key to firmly tighten the grub screws in the front of the base brackets.
Do this firmly |
If you are attaching your SmartFold to an Evolution E2 Bench see section 2.4 to find out how to attach the cutter arms to an Evolution E2 Bench >
If the black brackets support both arms of the cutter use the black steel bar (part * – supplied with the SmartFold Bench).
Pass the long countersink screw (supplied with the bench) through the arm and black support bracket then use the 2.5mm Allen (hex) key to loosely attach into the clamp bar. Repeat the step on the other side of your machine.
Do this gently |
Pull and remove end stop.
Slide the cutting head to the right.
Gently lift to remove the cutter head, then replace end stop.
Grip the cutter bar firmly, lift carefully and swing over the edge of the bench, bring gently to a stop when vertical.
Be careful when lifting |
Insert long countersink screw (supplied with the bench) but do not fully tighten. Repeat this step on the other side of your SmartFold.
Do this gently |
Use 4mm Allen (hex) Key to loosen the cap screws by one full turn at the end of the SmartFold.
DO NOT loosen the domed head screws that have red paint on them.
Repeat this step on the other end of your SmartFold.
Next step:
If you are attaching your SmartFold to an Evolution3 SmartFold Bench see section 2.3 to find out how to attach the cutter arms to an Evolution3 SmartFold Bench >
You will need this part to attach your SmartFold to an Evolution2 Bench.
Lift the stepped clamp bar (part D) into position as shown.
Pass the long countersink screw (supplied with the bench) through the arm and black support bracket then use the 2.5mm Allen (hex) key to loosely attach into the clamp bar. Repeat the step on the other side of your machine.
Do this gently |
Pull and remove end stop.
Slide the cutting head to the right.
Gently lift to remove the cutter head, then replace end stop.
Grip the cutter bar firmly, lift carefully and swing over the edge of the bench, bring gently to a stop when vertical.
Be careful when lifting |
Insert long countersink screw (supplied with the bench) but do not fully tighten. Repeat this step on the other side of your SmartFold.
Do this gently |
Use 4mm Allen (hex) Key to loosen the cap screws by one full turn at the end of the SmartFold.
DO NOT loosen the domed head screws that have red paint on them.
Repeat this step on the other end of your SmartFold.
Next step:
The width of the work surface needs to be 40cm (15 ¾″) wider than the cut length of the SmartFold.
Example: E3SF260 (104″) + 40cm (15 ¾″) = 300cm (118″) work bench
Check the flatness of the worktop by stretching a thin piece of strong thread between two blocks of the same height approximately over the area the cutter is to be mounted.
Measure the highest and lowest part of the worktop under the thread, the difference between the two measurements should be no more than 3mm (⅛″). If it is greater it will be necessary to adjust the surface flatness with a new top or by using spacing pieces under those base brackets (part B) that require it when they are installed.
The spacing pieces (part S) should be made from 1.5mm – 3mm (1⁄16″ – ⅛″) thick rigid material such as ACP or PVC Foamboard cut to the same size as the base bracket and placed under the base brackets (part B) as they are installed (next section).
The work surface must be stable with a robust framework below and good support (no flexing) in the area under the two ends of the cutter.
Both ends of the cutter must be fully supported and not overhanging the work surface.
In this section you will need base brackets (part B) and short posi head screws (part C).
Place the first base bracket (part B) 18cm (7″) from the edge and 9.5cm (3 ¾”) from the front of your bench. Use a Posi head screwdriver to tighten screws.
Place the following base brackets (part B) 43.5cm (17 ⅛″) from the edge of the previous base bracket and 9.5cm (3 ¾”) from the front. Use a Posi head screwdriver to tighten screws.
Continue placing the rest of the base brackets in this way.
NOTE: If you had to place spacing pieces under any of the base brackets it is recommended the thread is used (as seen in the work bench flatness test – (see 3.2 to find out how to do the flatness test >). Measure to the top surface of each base bracket to check they differ by no more than 3mm (⅛”).
Centralise and lower the cutter slowly onto the base brackets.
Once the SmartFold is in place, use scissors to remove the film packaging.
The base brackets have 2 grub screws each located at the front and the back (see ‘ x’ and ‘ y’).
Use the long end of the 3mm Allen (hex) key rotate the grub screws in the front of the base brackets until you feel them come to a stop, do not tighten any further.
Do this gently |
Repeat the process on the grub screws at the back of the base brackets.
Do this gently |
Use the 3mm Allen (hex) key to firmly tighten the grub screws in the front of the base brackets.
Do this firmly |
Take the long screws (part D) and a Posi head screwdriver to the highlighted section of the SmartFold.
Fix the arm to the work surface but do not tighten at this stage. Repeat on the other end of your SmartFold.
Do this gently |
Pull and remove end stop.
Slide the cutting head to the right.
Gently lift to remove the cutter head, then replace end stop.
Do this gently |
Grip the cutter bar firmly, lift carefully and swing over the edge of the bench, bring gently to a stop when vertical.
Be careful when lifting |
Insert the highlighted screw but do not tighten. Repeat this step on the other side of your SmartFold.
Do this gently |
Use 4mm Allen (hex) Key to loosen the cap screws by one full turn at the end of the SmartFold.
DO NOT loosen the domed head screws that have red paint on them.
Repeat this step on the other end of your SmartFold.
Ensure the flat face of the lever is facing to the centre of the unit.
Insert the handle between the body of the cutter bar and the steel plate that can be seen within opening.
TIP: You can use the 3mm Allen key to move the steel plate within the opening if you are struggling to insert the handle.
Use the 5mm Allen (hex) key and insert it into highlighted section. Tighten fully.
Do this firmly |
Repeat these steps on the other end again ensuring the flat face of the lever is facing to the centre of the unit and the handle is inserted between the body of the cutter bar and the steel plate. Tighten the fixing screw firmly.
Use an 8mm spanner/wrench to adjust the highlighted nut to obtain the best setting to hold or hover the cutter bar above the base plate.
Loosen the nut a small amount, raise the cutter bar using the lever then carefully release the lever and the cutter bar should lower itself to the base plate. If not loosen the nut a small amount more.
Raise the cutter bar and tighten the nut a very small amount until the cutter bar is held from falling.
Nudge the lever towards you in small movements, if the cutter bar then falls tighten the adjustment nut a very small amount and try again.
Insert a piece of A4/letter paper under the cutter bar at one end, push the lever away from you to fully lower the cutter bar. Test the paper is clamped by trying to move it.
Repeat over the length of your SmartFold and take note of the areas where the paper moves when you pull it.
In those areas that the paper is not clamped, use the 10mm spanner/wrench to adjust the hex screws underneath the adjacent base brackets. There are two adjustment screws on each base bracket and they must both be adjusted by the same amount. Turn the hex screw just enough to correct the clamping in that area.
Access rear hex screw from the back of the machine. Adjust by the same amount as above.
Repeat the clamping check along the whole length of the cutter bar, make further adjustments until the paper is clamped along the whole length of the machine.
Using a Posi screwdriver (if fitting to custom made bench) or 3mm Allen (hex) key (if fitting to a SmartFold bench) fully tighten the vertical screws fixing the arm to the work surface (two at each end of the SmartFold).
Use 4mm Allen (hex) key to tighten the two cap screws, one located at each end of the SmartFold.
DO NOT loosen or tighten the red painted dome head bolts.
Repeat this step on the other end of your SmartFold.
If fitting the SmartFold to a custom-made worksurface build the surface up behind the base plate by 15mm (⅝”) using MDF, plywood or similar, to level the work surface with that of the cutter.
When fitting to a SmartFold Bench, the 18mm (¾”) thick bench worktop should now be installed.
Registering your SmartFold machine will activate your 5 year guarantee.
See the Evolution3 SmartFold User Guide for advice on cutting techniques, using the different cutting heads and care and maintenance of your machine.
The Evolution3 SmartFold (part A) comes in 6 different sizes ranging from 1.1m (44″) to 3.6m (144″)(cutting length) in 0.5m (20″) increments. Each machine is fitted with a Double Graphik blade cutting head.
E3SF110: 3 x B 6 x C
E3SF160: 4 x B 8 x C
E3SF210: 5 x B 10 x C
E3SF260: 6 x B 12 x C
E3SF310: 7 x B 14 x C
E3SF360: 8 x B 16 x C
The three pieces of ACP (aluminium composite panel) or PVC foamboard should be approximately 150mm x 100mm (6″ x 4″) and 3mm (⅛″) thick.